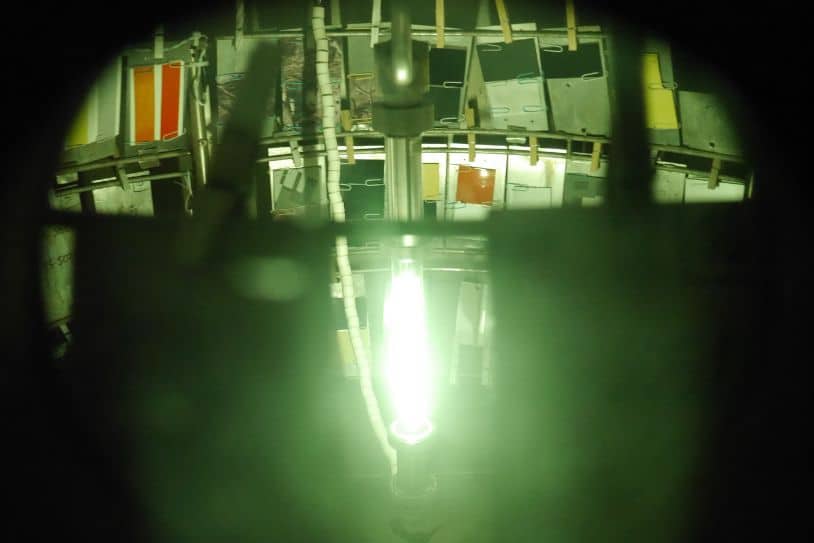
Using Xenon Arc in Material Testing: Combining Performance and Durability
Xenon arc testing has become a fundamental technique in material testing to evaluate their resistance to ultraviolet (UV) radiation, which is essential in industries ranging from automotive to aerospace and consumer goods. This method, which includes standards such as ASTM G155, ASTM D2565, ASTM D4459 ASTM D5071 and ASTM D6695, not only provides exceptional performance in simulating extreme environmental conditions but also highlights significant environmental benefits. Let’s dive into how xenon arc testing is revolutionizing the assessment of material durability and sustainable industrial practices.
Understanding Xenon Arc in Material Testing
Material tests involving xenon arc simulate the effects of sunlight and weather exposure. In this process, a xenon arc lamp is used to generate exposure similar to that of the sun, along with controlled temperature and humidity conditions, all accelerated.
Material samples are exposed to this intense light for extended periods to determine their resistance to fading, degradation, and other forms of damage. Standards such as ASTM G155 specify practices for using a xenon arc apparatus for exposing non-metallic materials, while ASTM D2565 focuses on the exposure of plastics intended for outdoor applications.
Applications of Xenon Arc Material Testing
Xenon arc material testing is widely used across various industrial sectors, including:
- Automotive Industry: The automotive industry uses xenon arc tests to evaluate the resistance of paints, plastics, and textiles to outdoor and indoor conditions (depending on the test parameters used).
- Construction Industry: In the construction industry, xenon arc tests are used to assess the durability of building materials exposed to UV rays and weather conditions, such as exterior coatings.
- Consumer Products Industry: The resistance of packaging, coatings, and decorative materials to environmental conditions is among the assessments conducted by xenon arc tests in the consumer products industry.
- Aerospace Industry: Materials used in the aerospace industry, such as composites and coatings, are subjected to extreme conditions of UV radiation and climatic variations. Xenon arc tests ensure their durability and performance by simulating these harsh environments.
Environmental Benefits of Using Xenon Arc
Using xenon arc in material testing provides a reliable and efficient method to evaluate the durability and resistance of materials to extreme environmental conditions. In addition to its remarkable performance, this method offers significant environmental benefits, contributing to sustainability and environmental responsibility across various industrial sectors.
- Equipment Durability: The equipment used for xenon arc material testing is often designed to be durable and reliable, reducing the need for frequent replacements and thereby contributing to the reduction of electronic waste.
- Resource Optimization: By assessing material durability from the design phase, xenon arc material testing allows companies to select more durable materials, contributing to long-term resource conservation.
The advent of climate change will necessitate more frequent use of such testing as environmental conditions become increasingly challenging for materials to withstand.
As part of Micom’s extensive selection of UV tests, Xenon arc tests represent a major advancement in material durability assessment. They reliably simulate extreme environmental conditions and promote sustainable industrial practices. By adopting these tests, companies can enhance the performance and longevity of their products and contribute to a more sustainable and responsible future.
Explore Our Xenon Arc Testing Solutions
Ready to optimize the durability and performance of your materials while contributing to environmental sustainability? Contact us today to discover how our xenon arc testing solutions can transform your industrial practices. Together, let’s build a more resilient and sustainable future. Contact us to learn more and get a personalized consultation.